Ever since its introduction in the late 19th century,半岛app体育怎么样好用吗has revolutionized the way we create plastic products.Although the technology has evolved significantly over the years, many injection molds today still fall into two main categories: hot runner and cold runner systems.Each of these systems has their own benefits and limitations which make them better suited for specific applications.
Understanding the differences between these technologies can help you have a more productive and informed discussion with your plastic injection specialist to determine the most feasible option for your unique application.
Hot Runner MoldsHot runner molds consist of two plates that are heated with a manifold system.The manifold helps maintain a consistent temperature by keeping the molten thermoplastic in the runners at the same temperature as the heating cylinder.The heated runners deliver the molten plastic to nozzles that fill the core mold to form the final part.
The heated runner system is housed in a separate plate.This plate remains stationary during the molding cycle.The core molding plate then opens to reveal the final molded part without any runners attached.
There are several types of hot runner systems.In general, however, they fall into two main categories!externally heated and internally heated.The externally heated systems are well suited to polymers that are sensitive to thermal variations. Internally heated systems offer better flow control.
The hot runner process eliminates runners entirely, so recycling and regrind (which can only be done with virgin plastics) do not impact cycle times.A variation on this system is known as an insulated runner.The insulation, rather than heat, keeps the plastic in a molten state.This system can only accommodate a few types of plastics—specifically semi-crystalline polymers, which tend to have a low thermal conductivity.
What Is a Cold Runner Mold?
Cold runner molds usually consist of two or three plates that are held within the mold base.The molten thermoplastic is first injected into the mold from a nozzle via the sprue, which fills the network of runners that lead to the mold cavities.In this system, the runners are unheated and act as a delivery system that distributes the molten plastic to the individual molding cavities.The cold runner system subsequently cools the sprue, runner, and gate along with the molded part.
In two-plate molds, sprue and the runner system remain attached to the final product.An ejection system is then used to separate the molded component from the core half of the mold.For those of you who assembled a model car at some point in your youth, the runners and the parts were not separated.The child assembling the model was responsible for that final part of the process.
In three-plate molds, a stripper plate contains the sprue which delivers the molten thermoplastic to the network of runners which are contained in a separate cavity plate.The final molded part is formed and cooled on the core half of the plate without any runners or gates attached.The three-plate mold system automatically separates the runner from the part as the mold opens.In both the two-plate and three-plate mold systems, the runner may be reground and recycled, thereby reducing plastic waste.
How to Manufacture the Perfect Plastic
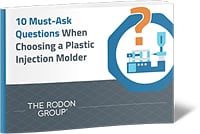
10 Must-Ask Questions eBook
What you need to know before selecting a molder for your project
Download our eBook, "10 Must-Ask Questions When Choosing a Plastic Injection Molder." Inside, we cover key questions like:
- Does the molder guarantee the molds for the life of a project?
- How many molding machines do they have and what are their capabilities?
- Is their pricing competitive, even when comparing with offshore molders?
Hot Runner Molds vs Cold Runner Molds
Hot runner systems generally possess significantly faster cycle times than cold runner systems.The elimination of the runners greatly reduces the number of post-production activities such as runner and sprue removal, regrinding, and recycling.The lack of runners also reduces potential waste during the molding process and eliminates the need for robotics to remove runners.This contributes to an overall cost reduction and increases the efficiency of the mold automation process.
Also, because each runner feeds a dedicated mold, hot runner systems are capable of fabricating larger parts.Hot runners, however, tend to be more expensive than cold runner injection mold systems.Because each hot runner feeds into a dedicated mold, additional internal or external heating sources are required to keep the runners at a consistent temperature.
Additionally, thetooling costis usually higher than that of cold runner systems.As a consequence, molded parts can be more expensive to produce, thereby increasing the cost of the total production volume.The complex nature of the hot runner equipment also means that it requires more careful inspection and maintenance, leading to an increase in maintenance costs and potential downtime.Also, internally heated hot runner systems may not be suitable for thermally sensitive polymers since there are areas where material could stick to the surface and become overheated.
Cold runner systems are, typically, relatively more cost effective than their hot runner counterparts.The total cost to produce a molded item and lower general maintenance expenditures both add to the overall reduction in cost.They are also capable of handling a wide variety of commodity and engineered thermoplastics.Additionally, cold runners are more flexible than hot runners since runner and gate locations can be easily changed or upgraded, allowing for faster design changes.
However, one of the significant disadvantages of cold runner systems is the actual production of the runner itself.In two-plate cold runner systems, the runner needs to be manually separated from the finished part after each run.If these runners are not reground and recycled, the plastic material is wasted after each run.Furthermore, the removal of the sprues and runners – and the time it takes to recycle each runner – adds to the cycle time, resulting in a slower production time than hot runner systems.
半岛平台下截链接If you would like to learn more about which plastic mold injection technique is right for your application,download our free eBook, or feel free to contact our technical team.
Comments