Capabilities
半岛真人赌城The Rodon Group is world-renowned for the production of injection molded components of the highest quality and precision at highly competitive prices.From concept to completion, we provide all of the necessary resources to promptly and accurately complete your project.
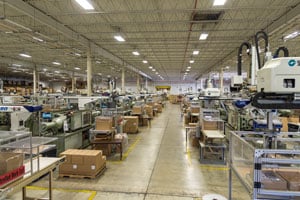
半岛真人赌城Rodon utilizes the latest design software, builds your stainless steel tool in our CNC driven tool room and manufactures your parts in our automated125 press facilitywith quality checks along every step of the process.
We serve adiverse group of industriesincluding windows and doors, medical and pharmaceutical, consumer products, construction and food & beverage.
半岛真人赌城The Rodon Group Difference
半岛app体育怎么样好用吗At Rodon, we are proud of the reputation we have built in the plastic injection molding industry, a reputation for high-quality, just-in-time, precision parts manufacturing.Our state-of-the-art facility is equipped with the latest in automation, scheduling and quality inspection technology.We partner with only world-class suppliers.The resources of our supplier base, in addition to our in-house capabilities, provide a customized manufacturing solution.
半岛真人赌城See each step of The Rodon Group's plastic part production process and our obsessive attention to achieving perfect parts!
半岛app体育怎么样好用吗Plastic Injection Molding Design
半岛app体育怎么样好用吗Plastic injection molding is a method of producing high-volume precision parts at a low cost.This versatile process can create even highly complex or intricate shapes precisely and efficiently.To ensure success, developing a precise and moldable design is critical.The most effective mold designs are optimized for consistent wall thickness and ease of ejection, among other factors, while keeping manufacturing costs in mind.
半岛真人赌城Rodon engineers have over 25 years of experience in designing and building molds.半岛app体育怎么样好用吗This extensive background gives our team the expertise necessary to develop creative solutions for even the most challenging design manufacturing problems. In plastic injection molding, several design factors are particularly crucial for ensuring finished product moldability, quality, and cosmetic appeal.Wall thickness, ribbing, and boss design are all key focus areas for proper part design.
Wall Thickness
Achieving uniform wall thickness is crucial as it will eliminate most of the possible manufacturing defects by ensuring the mold fills and cools correctly.Melted plastics flow into areas of least resistance first.This means that thick-walled areas are the first to fill.
Ensuring a mold design features uniform wall thickness will improve a part's strength, weight, and aesthetics.Parts that are too thick frequently result in unsightly warping, sink, or internal voids.Part uniformity can be maintained by coring or hollowing out thicker regions in the part design.
Ribbing
Ribbing is a crucial component of a part's overall strength, as it supports the walls and other dimensional components.Ribbing typically makes up 50% to 70% of a wall's total thickness, as any greater percentage risks sinking.A part that is intended to be structural should contain ribs as well as supporting gussets if properly designed.These increase strength and help eliminate cosmetic defects, such as voids, sink, and warp.
Bosses
Bosses accommodate assembly through pins or screws.They should be the same thickness as ribs and also require draft to aid in ejection.
Toolmaking
High-quality, precision molds take time and exceptional accuracy to build.They are designed to last for years and can represent a large investment in the manufacturing process, particularly when large-volume manufacturing and complex tooling are involved.Choosing a knowledgeable and reliable toolmaker is essential.
半岛真人赌城The Rodon Group fabricates the best tooling in the industry, with an exceptional tool warranty to reinforce these claims.We design tools for high-volume, low-tolerance production over the lifetime of your project.As long as we are running a tool that we built, there will never be any maintenance or repair charges.All of our tools are constructed from stainless steel mold bases and cavities, ensuring optimal durability and performance.
半岛app体育怎么样好用吗Plastic Injection Molding Manufacturing
After a production mold is finalized and the machine has been prepped, manufacturing can begin.We perform an initial run to thoroughly examine components for any part defects.When no defects are found, full production can begin.半岛真人赌城Rodon carries acomprehensive selectionof injection presses that are classified based on clamping pressure.The machine used depends on many variables, including the type of resin selected, mold size, and the number of cavities.
Depending on the part and the molder's agreement, quality checks take place on a regular basis.These checks inspect for:
- Color correctness
- Strength
- Flash
- Warping
半岛app体育怎么样好用吗Plastic Injection Molding Automation
半岛真人赌城Rodon uses an MRP (Material Requirement Planning) system.This tool allows our manufacturing team to monitor all jobs from the minute they are initiated to the time they are delivered, including all downstream impacts.Our facility of 125 presses runs 24 hours a day, 7 days a week for maximum efficiency.
半岛app体育怎么样好用吗Plastic Injection Molding Materials
半岛app体育怎么样好用吗Understanding the differences between plastic injection molding materials is crucial for selecting the most appropriate material for a given application.When selecting the best material for your project, it's important to consider factors such as the end-use environment, desired final appearance, and what industry-specific regulations need to be met.
We expertly help our clients select the most appropriate material for their projects, for high-performing yet cost-effective results.半岛app体育怎么样好用吗While many types of plastic resins are used in the plastic injection molding process, the top five most common plastic types include:
- Acrylonitrile Butadiene Styrene (ABS)
- Celon® (Acetal)
- Low-density polyethylene (LDPE)
- Polypropylene
- High Impact Polystyrene (HIPS)
Fulfillment and packaging
We pride ourselves on providing Just-in-Time manufacturing to suit the fulfillment demands of each client.Quality control checks are performed as components are sorted, weighed, and sealed for stock or shipment.In keeping with our commitment to automation and conservation, our servo robots provide custom stacking and packing to minimize cartons and freight charges.
Industries
半岛真人赌城With over 65 years of experience creating custom plastic parts for customers throughout diverse industries, The Rodon Group has a unique perspective on manufacturing high-quality, high-volume parts at the lowest possible cost.We pride ourselves on identifying the most high-performing and cost-effective solution for each client.
The industries we serve include:
- Construction
- Food and beverage
- Medical
- Pharmaceutical
- Window and door
- Household appliance
We have expertise in creating components for a diverse portfolio of goods.Our past experience includes everything from bearings and custom housings and fasteners, to bed frames, lawn and garden supplies, point-of-purchase displays, and more.You can view images of our industry-specific part exampleshere.
半岛app体育怎么样好用吗Contact The Rodon Group for Plastic Injection Molding Services
半岛app体育怎么样好用吗At The Rodon Group, high-volume, customized plastic injection molding is our specialty, and our projects are world-renowned for their quality and precision.半岛app体育怎么样好用吗With decades of experience in thermoplastics and a dedication to technological innovation, we are a trusted provider of high-quality plastic injection molding services.We specialize in strong plastic materials and offer guidance on industry-diverse applications.Our team can create a high-performing solution that matches your exact requirements.半岛平台下截链接Learn more bycontacting ustoday, orrequest a quoteto get started on your next project.
半岛app体育怎么样好用吗A summary of our plastic injection molding capabilities:
半岛app体育怎么样好用吗Plastic Injection Molding General Capabilities | Custom Molding Solutions Problem Solving Design Tool Manufacture |
Product Capabilities | Small Parts |
Mold Process Type | Injection |
Equipment | Automated Robotic Microprocessor Controlled Self-Diagnostic |
Material | Engineering Grade High Temperature Commodity Resins ABS Celcon Glass Filled Nylon PVC HDPE LDPE PP POM HIPS TPE TPR Nylon Acetal Others |
Clamping Force | 46 to 720 tons |
Shot Size | Fractional to 107 oz. |
Number of Cavities | Prototype to 100+ |
Length | Up to 10 in |
Width | Up to 10 in |
Height | Up to 10 in |
Inspection | Visual Systems Product Tolerances Color Monitoring Physical Appearance Certified Mechanical Inspection |
Testing | Gauges Surface Plates Scales Tensile Strength Ultra Violet (UV) |
Quality | Control Checks Specifications SPC Charting Documentation Quick Vision System |
Additional Services | Project Management Custom Packaging Design for Manufacturability In-House Tooling |
Production Volume | 500,000 parts and up |
Lead Time | Parts shipped from stock to less than 2 weeks (Production) 4-6 weeks- smaller, up to 12 weeks- larger (Tooling) Just In Time (JIT) Safety Stock Program |
Additional information
Industry Focus | Consumer Products Medical/Pharmaceutical Food/Beverage Construction/Building Point of Purchase Displays Bearings/Conveyers Office Products/Cabinets/Hardware Baby/Children's Products Lawn/Garden Shower/Bath Products Windows/Doors |
Intended Application | Custom parts for various applications |
Quality Certifications | ISO 9001:2015 OSHA |
Resin Certifications | FDA RoHS Reach NSF |
Efficiency | Landfill-Free Facility Lean Manufacturing Demand response program |
File Formats | AutoCAD SolidWorks IGES |