半岛app体育怎么样好用吗Plastic Injection Molding Explained
In manufacturing, molding refers to the process of shaping a type of pliable material or liquid by using a rigid matrix or mold.半岛app体育怎么样好用吗In plastic injection molding, raw polymer resin granules are melted into a liquid and injected into a mold, where the plastic takes the desired shape.Varying levels of heat and pressure may be applied to create the final profile for the end product.
半岛app体育怎么样好用吗The basic plastic injection molding process consists of the following steps:
- Plastic resin materials enter a barrel.
- Heat melts the plastic, which is mixed together.
- Shot sizes are created, determining the volume of material to be injected into each mold.
- The mold closes.
- The melted plastic is injected into the mold cavity.
- While the material cools and solidifies, the injection molding machine prepares steps 1 to 3 for the next cycle.
- The mold opens.
- The part is ejected.
- The process repeats when the mold closes again.
In today's ever-evolving world of manufacturing, plastics are being used to make everything from automotive body parts to synthetic human body parts.To create critical components and ensure optimal performance, many manufacturers choose to半岛app体育怎么样好用吗make use of plastic injection molding.
To suit diverse industry needs, there are several other types of plastic molding available, each offering unique features and benefits.An application's particular specifications and requirements will determine which type of molding process is best-suited for a specific part.
Below are a few of the most common different styles of plastic molding.
Blow Molding
Theblow molding processfollows the same basic steps found in the art of glass blowing.To blow mold a part, the manufacturer inflates a parison — a heated plastic mass, usually in the shape of a tube — with air.The parison inflates until it fills the mold and conforms to its shape.In this way, the plastic is blown into its desired form.Once cooled, the newly formed plastic part is ejected from the mold.
Blow molding is especially useful for economically manufacturing one-piece, hollow objects in large volumes, as the process can quickly create uniform, thin-walled containers — perfect for small objects like bottles, as well as larger ones like storage containers and drums.
Depending on the specific application, manufacturers can use a variety of thermoplastics in blow molding to create a more customized product.Commonly worked materials include low-density polyethylene, high-density polyethylene, polyethylene terephthalate, polypropylene, and polyvinyl chloride.
Compression Molding
Compression molding involves placing a heated plastic inside of a heated mold, then closing it to compress the plastic into the desired shape.Once cooled, the part is removed from the mold.The heating process, called curing, helps ensure that the final product will maintain its integrity and shape.Compression molding offers many unique advantages!it's both cost-effective and highly efficient.The process is also quite versatile, allowing manufacturers to create parts that vary greatly in thickness, length, and intricacy.
Because compression molding often uses advanced composites for the plastic material, the process yields stronger, more durable parts, making it popular across a range of different industries.For example, compression molding often employs high-strength materials, such as thermosetting resins, fiberglass, and reinforced plastics, resulting in products that are sturdier and more resilient than those offered by other molding processes.
Allowing for the creation of high-strength parts, compression molding is used to produce components for a vast range of applications, including automotive parts, household appliances, clothing fasteners, and body armor.
Extrusion Molding
While other forms of plastic molding use extrusion to insert the plastic resins into the mold, extrusion molding extrudes the melted plastic material directly into the die.This process is unique in that the shape of the die, not the mold, determines the shape of the final product.
Extrusion molding is ideal for manufacturing parts with continuous length and uniform cross-sections.半岛app体育怎么样好用吗Similar to a plastic injection molding machine, the extrusion molding machine has a screw that turns to feed the plastic resin into the feeder.The molten plastic then moves through a die, creating a long, tubular shape.The shape of the die determines the shape of the plastic tube.Once the extrusion is cooled, it is removed from the machine.
Extrusion molding is well-suited for long, hollow-formed applications, such as tubes, pipes, and straws.Plus, manufacturers can create these parts in many different shapes, including T-sections, U-sections, square sections, I-sections, L-sections, and circular sections.
Injection Molding
Of the various molding processes available,半岛app体育怎么样好用吗is considered to be the most versatile, as it can be used to create a variety of parts, ranging in both size and shape.Presses also come in different sizes, based on the pressure they exert and their tonnage.
Injection molding basic principles are fairly simple, butthe actual process can be quite complexwhen it comes to maintaining part consistency.The process involves the injection of melted plastic into a mold, which is made of steel.The mold itself has cavities that will form the parts!once injected, the molten plastic fills the cavities and the rest of the mold.Once cooled, the parts are ejected by pins.
Thanks to its excellent versatility, injection molding can be used to create everything from large automotive parts to small, intricate parts used in surgical equipment.Injection molding also allows for a high level of customization, as various plastic resins and additives can be used, allowing designers and engineers to create unique parts to meet highly complex or unusual application needs.And there are some enhancements and techniques available — such as an array of resin and finish options — for manufacturers looking to create even more specialized parts.
Though it can be expensive to initially make the molds themselves, once built, the production costs become quite low.In fact, injection molding is best-suited for the creation of very high volumes of precise parts!once production begins, the cost per part drops significantly, making the process very economical for high-volume runs.
半岛app体育怎么样好用吗is a highly reliable solution for producing large numbers of precise, consistent components.It's also more efficient and cost-effective than other molding styles, in that it produces much less waste.As a result, injection molding is most often used for the manufacture of high-quality parts in high volumes.
Rotational Molding
Rotational molding, also known as rotomolding, uses high temperatures and rotational movement to coat the inside of a mold to form a part's desired shape.First, the mold is filled with a polymer powder.The heated mold then rotates on two perpendicular axes so that the powder adheres to the entire interior of the mold.As it continues to rotate, the mold eventually cools and is removed, ultimately forming an even-walled component.
Rotational molding is best suited for the creation of large, hollow, one-piece containers, such as tanks.Though cost-effective, it is not a fast-moving process.However, rotomolding wastes little material, and what excess material is produced can often be reused, making it an economical and environmentally friendly manufacturing process.
Other key advantages include the ability to produce parts with consistent wall thicknesses, enhanced design flexibility, and great strength
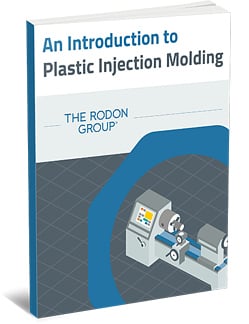
半岛app体育怎么样好用吗Intro to Plastic Injection Molding eBook
半岛app体育怎么样好用吗Explore the World of Plastic Injection Molding with Confidence
半岛app体育怎么样好用吗Download our eBook, "An Introduction to Plastic Injection Molding." Inside we cover:
- Types of plastic molding, their benefits & applications
- Types of presses and their capabilities & advantages
- 半岛app体育怎么样好用吗How to determine plastic injection molding costs
- Common mistakes to avoid
半岛平台下截链接
Each of these plastic molding processes offers unique features and advantages, making each style well-suited for different types of applications.
At半岛真人赌城The Rodon Group, our designers and engineers are well-versed in custom,high volume半岛app体育怎么样好用吗plastic injection molding and work closely with all of our clients to ensure their unique needs are met.In most situations, there are several ways to approach a manufacturing challenge, and we can provide expert insight into the various techniques and materials best suited to a specific project.
半岛app体育怎么样好用吗To learn more about plastic injection molding and how it can help with your next project, download our free eBook, "半岛app体育怎么样好用吗Plastic Injection Molding 101."Contact usorrequest a quoteto start your solution.
Comments