Design engineers have various options when choosing a半岛app体育怎么样好用吗process to best suit their specific application.Each of the three primary methods — hydraulic, electric, and hybrid — feature unique benefits and drawbacks.To make the right selection for your project, it's important to have a full understanding of how these methods differ and what they can offer you.
半岛app体育怎么样好用吗Hydraulic Plastic Injection Molding
半岛app体育怎么样好用吗First coming into existence in the late 1930's, hydraulic plastic injection molding machines (IMM's) once dominated the market, but their dominance has been impacted since the introduction of all-electric machinery in the 80's.However, hydraulic machines may still be the best option for the job depending on your specific needs, electricity costs, and personal preferences.
These types of machines employ hydraulic cylinders to clamp together two halves of a mold at high pressure.Plastic substrate pellets are then melted, and the liquid is injected into the mold cavity.Once the plastic has cooled and hardened, the mold halves are separated, the part is extracted, and the process is repeated.
To prevent the mold from being pushed open by injection pressure causing excessive material to "flash" around the parts, the clamping unit must be able to supply enough locking force to keep the mold shut during injection.Roughly 3-4 tons of clamp force per square inch of cavity is needed for parts with thin wall sections and deep draw depths.For thick wall sections and shallow draw depths, about 2 tons per square inch is needed.
Today's hydraulic IMMs are able to control clamp forces up to and exceeding 8,000 tons and can create parts weighing in at more than 50 pounds.Hydraulic molding is a popular choice for the automotive industry, which requires the production of large, heavy parts such as bumpers.
Advantages
Hydraulic injection molding is the preferred option for actuating core pulls, ejectors, and valve gates, as well as thick-walled parts that require long hold times.Some of its benefits over all-electric machines include:
- Greater clamp force for large parts
- Better injection rates
- High resistance to wear and tear
- Larger shot size
- Better ejection capability
- Available with gas accumulators to make up for slower clamp movements
- Lower initial purchase price
- Low cost and high availability of replacement parts, resulting in lower maintenance costs
- Easier to control for high-level projects
- There are many units available on the used market because of this method's popularity
Disadvantages
Because they're so powerful, hydraulic machines consume large amounts of energy even when idle.While a typical electric machine may consume about 2.55 kWh during an injection molding process, hydraulic machines may consume 5.12 kWh.They require higher temperatures for molding and more time for cooling, and they're not ideal for clean rooms because of the risk of fluid leakage.
Hydraulic IMMs are also noisier and less precise than all-electric presses.However, as clamp forces increase and control systems improve, hydraulic machines' precision performance also improves.
半岛app体育怎么样好用吗Electric Plastic Injection Molding
Introduced in 1984 in Japan, all-electric injection molding machines are relatively new to the market but, after rapid adoption, now account for over half of all IMM machines sold in the United States.
These machines are powered by digitally controlled high-speed servo motors rather than hydraulics, allowing for a faster, repeatable, more precise, and energy-efficient operation.Electric machine operation is highly predictable, so once a desirable injection process has been reached, it can be replicated very consistently, resulting in higher quality parts.Once a job has been programmed into an electric machine, its digital controls allow it to run virtually unattended, which lowers labor costs and boosts profits.
Advantages
Since it poses no risk of oil contamination, electric injection molding is well-suited for cleanroom applications.Because of its high precision, this process is also ideal for small- to medium-sized parts and medical products such as Petri dishes and syringes.Other advantages include:
- Tight precision and repeatability with reduced scrap rates
- Cleaner process that never leaks fluid
- Lower downtime commonly associated with hydraulics
- Energy savings from 30% to 70%
- Quieter operation!reduced motor noise below 70 dB
- Higher rapid injection speeds up to 800 mm/sec and faster clamp motion
- Shorter startup time and up to 20% faster cycle times
- Lower unit cost with less material waste
- Requires no consumables such as oil that would need to be replaced or cleaned
- Lower power requirements result in significantly lower operating cost
Disadvantages
Although electric machines are faster, cleaner, and moreenergy efficient, they are unable to achieve the clamp forces produced by hydraulic machines and also come with a higher initial cost.They are toggle-clamp machines that are driven by ball-screws, both of which are wear items, and can be expensive to replace or difficult to find on the used market.And, despite lending great precision, the high positioning accuracy of electric machines can make them less forgiving when compared to hydraulic presses.
半岛app体育怎么样好用吗Hybrid Plastic Injection Molding
Combining the best of both worlds, hybrid injection molding machines have been on the market for a few decades now, and combine the superior clamping force of hydraulic machines with the precision, repeatability, energy savings, and reduced noise of electric machines.This allows for better performance for both thin- and thick-walled parts.These machines have become increasingly popular over the last few years due to their efficiency and ease of use.半岛真人赌城Here at The Rodon Group, we recently addedseven hybrid presses to our lineup, and now have 23 total.
Nearly 66% of energy in a hydraulic press goes toward screw recovery.So while hybrid presses are more costly upfront, their electrified screw rotation can result in significant savings, which can then be passed on to customers.Our hybrid machines have all the force delivered by full-hydraulic machines, with virtually the same energy-efficiency of an all-electric.
Advantages
半岛app体育怎么样好用吗Hybrid plastic injection molding is an energy efficient and long-lasting process without as much demand, all of which leads to a faster return on investment.Some of their specific advantages include:
- Continuous adjustments allowed by the servo pump
- Diversity of product design
- Tends to use a two clamp system over toggle
- Median upfront cost of all three options (hydraulic, electric, hybrid), but could provide the most long-term savings
- Closed loop process with faster response time
- Lower temperature requires less cooling and enables longer oil and machine life
- Faster time to ROI because of these efficiencies
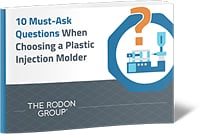
10 Must-Ask Questions eBook
What you need to know before selecting a molder for your project
Download our eBook, "10 Must-Ask Questions When Choosing a Plastic Injection Molder." Inside, we cover key questions like:
- Does the molder guarantee the molds for the life of a project?
- How many molding machines do they have and what are their capabilities?
- Is their pricing competitive, even when comparing with offshore molders?
Disadvantages
Because all hybrids are different, it can be difficult to match the correct press to the product, as well as secure replacement machines for certain applications.And if any maintenance is necessary for a hybrid machine, the supervisor must have knowledge of both hydraulic and electric presses.
半岛真人赌城How The Rodon Group Can Help
There's no one size fits all answer to which type of injection molding is right for you.For certain molding jobs, all three methods could even work equally well, but it's still important to understand their differences as they relate to your project.
No matter what your specific application, an injection molding machine — whether hydraulic, electric or hybrid — should provide you with reliable, high-quality parts while keeping costs down.To meet your unique needs,半岛真人赌城The Rodon Grouphas 118 Nissei presses at our facility, 75% of which are hydraulic, 20% hybrid, and 5% all-electric.
半岛平台下截链接To learn more about our capabilities or to discuss how our fleet of injection molding machines can help you with your high-volume production needs,reach out to us today.
Comments