半岛app体育怎么样好用吗In the plastic injection molding process, a stainless-steel part mold is filled with molten plastic, which then cools to form the final part.This manufacturing process offers a cost-effective method for producing large volumes of parts with consistent dimensions.半岛app体育怎么样好用吗Production volumes for plastic injection molding projects often range into hundreds of thousands or millions of parts.
While the initial tooling is more cost-prohibitive than many machining methods, the economies of scale gained in large production runs negate the initial set-up costs.The process also produces very little scrap and wasted thermoplastic material can be recycled back into the machine for use in production.
半岛真人赌城The Rodon Group has been at the forefront of thermoplastics manufacturing since its inception in 1956.We have 125 injection molding machines in our Pennsylvania facility, making us one of the largest family-owned and operated injection molders in America.
Injection Molding
半岛app体育怎么样好用吗Plastic injection molding remains the most versatile of plastic molding processes.A comprehensive range of injection molding machinery exists in differing tonnages or pressure ratings, and common material choices include multiple plastic resins and a broad range of additives used to alter the physical properties of final parts.Based on machine type and material choice, injection molding can produce items ranging from large automobile parts to small precision medical components.
半岛app体育怎么样好用吗While fabricating steel molds for plastic injection molding is expensive, this cost is offset by the low cost-per-part offered by the process.Low part cost, design flexibility, a variety of material and finishing options, and expansive customization techniques have made injection molding one of the most popular manufacturing processes available for engineers.
The standard injection molding manufacturing process follows these steps:
- Plastic is heated to its melting point.
- The melted plastic is injected into the mold with a nozzle until all cavities are filled.
- The mold is cooled, creating a finished part.
- The finished part is ejected from the mold automatically using pins.
半岛app体育怎么样好用吗Designing Plastic Injection Molding Parts
半岛app体育怎么样好用吗Developing a design for plastic injection molding is a complicated process that requires significant skill to avoid manufacturability issues.Proper design, planning, prototyping, and testing will help to prevent many of the pain points that can arise during the early phases of manufacturing.The right design will facilitate the production of high volumes of specialized, high-quality plastic parts without any costly delays or expensive defects.Designers or design contractors should account for the following aspects when creating a design for a plastic injection molded part:
- Boss design
- Corner transitions
- Gate placement
- Rib design
- Vent placement
- Wall thickness
- Weld lines
半岛app体育怎么样好用吗Material Selection for Plastic Injection Molding
Selecting the appropriate resin for a design is critical for the ultimate functionality of the final part.Recent advancements in polymer science have produced a comprehensive range of plastic resins that can facilitate a wide variety of mechanical and aesthetic properties in molded parts.
There are five factors to consider when choosing a plastic resin:
1.The aesthetic appearance of the part (color, texture, transparency)
2.The strength, stress, and flexibility/rigidity requirements of the part
3.Required resistances (temperature, chemical, weather, etc.)
4.Regulatory requirements (FDA, RoHS, REACH, NSF)
5.Part service life
With so many materials available, resin sourcing can be confusing.Working with an experienced injection molding provider ensures you'll get the correct resin for your design.
半岛app体育怎么样好用吗Fabricating Molds for Plastic Injection Molding
半岛app体育怎么样好用吗Constructing the molds used for plastic injection molding is the most time-consuming and expensive part of the process.These tools require a great deal of precision and specialized consideration by talented design engineers and toolmakers.An error in the mold could result in thousands of parts being ruined.As such, quality control and careful testing before full production are critical to project success.
半岛app体育怎么样好用吗While mold-making is the most expensive step in the plastic injection molding process, a quality precision mold will last for many years and can potentially facilitate the creation of millions of products.When creating a mold, there are multiple variables to consider, including:
- Core metal.Most high-volume molds are fabricated from stainless steel.The steel can be machined and fabricated to facilitate close tolerances and complex geometries, but still lasts for many years.半岛真人赌城At The Rodon Group, we still use many stainless steel molds that were created decades ago.
- Required cavities.Mold cavitations should be maximized to support higher efficiency during production.Also, using one mold per part in a multi-cavity tool typically facilitates uptime and high precision, while family molds tend to require significant maintenance and produce inferior parts.
- Mold base.A mold base is required to hold all mold cavities, components, and inserts in place during manufacturing.The cost of a mold base can vary wildly depending on customization requirements, size, and material.
- Machining.A variety of machining capabilities will be required to implement necessary customizations into the mold, such as cavities, cooling lines, cores, and ejectors.
- Complexity.More complex part designs will increase the ultimate cost of constructing a mold.
半岛app体育怎么样好用吗Plastic Injection Molding Costs
半岛app体育怎么样好用吗The start-up costs associated with plastic injection molding can vary wildly based on the complexity of the design.The injection mold itself is typically a significant investment—even more so if the design requires tight tolerances, intricate geometries, or if the mold has multiple cavities.Other factors that may influence overall costs include:
- Resin type
- Part size
- Cycle times
半岛app体育怎么样好用吗Ultimately, the costs of plastic injection molding scale downward as volume scales upward.半岛app体育怎么样好用吗This is why plastic injection molding is considered a high-volume process—the set-up costs are often too prohibitive for small and medium production runs.
半岛app体育怎么样好用吗The Plastic Injection Molding Manufacturing Cycle
半岛app体育怎么样好用吗Once you've committed to plastic injection molding as your process of choice, you'll need to source a quality provider for the service.半岛app体育怎么样好用吗At The Rodon Group, our plastic injection molding process follows these steps:
- Machine selection.We'll work with you to select the appropriate machine size for your mold and material choice.These machines are classified based on their tonnage rating, which refers to the amount of force they apply when clamping.半岛真人赌城At The Rodon Group, we have machines with capacities from fractional to 107 ounces and clamping force from 46 to 720 tons.
- Preparation.Once the mold is ready, and the machine and resin material is selected, an initial run can begin.
- Initial run.A small initial production run will undergo stringent quality assurance examinations to identify potential defects or other problems.Once the initial run has been cleared, full production begins.
- Full production.Once full production is underway, quality checks will continue at regular intervals to ensure no problems arise.Quality assurance measures check for common defects such as warping or flashing, part strength, and coloring issues.
- Inventory.Production planning based on your predictions and forecasts should ensure you have inventory when you need it.半岛真人赌城However, The Rodon Group understands that emergencies and unexpected sales peaks do happen.We keep safety stock on hand for every client to meet sudden demand spikes.
- MRP.We also strictly monitor all material inventories in real-time using our Material Requirement Planning (MRP) system.This lets us support client inventory planning initiatives and monitor jobs from planning through delivery.
Cold Runner vs.Hot Runner Molds
半岛app体育怎么样好用吗Plastic injection molding uses two different mold types: cold runner and hot runner.Each type has its benefits and drawbacks.半岛真人赌城The experts at The Rodon Group will help you determine which method is best for your project.
Cold Runner Molds
The mold base of a cold runner mold typically has two or three plates held within it.Plastic is injected into the mold using a sprue.This plastic fills up the runners and travels into the mold cavity.
- Intwo-plate cold runner molds,the runner system is attached to the mold, and an ejection system is in place to separate them.
- Inthree-plate cold runner molds,the runner is separated on its own plate, so only the finished part will be ejected.
In both two- and three-plate cold runner systems, these runners can be reground and recycled.This process increases overall cycle times but also reduces plastic waste.
Advantages of cold runner molds include:
- Cost-effective
- Low maintenance costs
- Can use many different polymer resin types
- Engineered or commodity
- Facilitates fast color changes
- Improved cycle times when robotic assist is available to remove runners
Disadvantages of cold runner molds include:
- Slower cycle times compared to hot runner systems
- Increased waste if plastic runners aren't recycled
Hot Runner Molds
Hot runner molds are built from two plates heated by a manifold system.The manifold heats the plastic, and then the mold cavities are filled with molten plastic via nozzles.
While a variety of hot runner systems exist, they can largely be split into two categories: internally heated and externally heated.
- Internally heated hot runner systems offer better control of plastic flow.
- Externally heated hot runner systems are best for polymers that are sensitive to changes in temperature.
Hot runner systems eliminate runners, so there is no need to recycle or regrind runner plastics.
Insulated runners are variations on the hot runner system which are used for injecting semi-crystalline polymers with low levels of thermal conductivity.Instead of using heat to keep the plastic in its melted state, the insulation on the runners keeps it from cooling.
Advantages of hot runner systems include:
- Less waste
- Potential for faster cycle times
- No need for automation to remove runners
- Can handle large parts
Disadvantages of hot runner systems include:
- Molds are more expensive to create
- Difficult to change colors
- High maintenance costs
- Higher potential downtime
- Often not suitable for thermally sensitive resins
半岛app体育怎么样好用吗Common Terminology in Plastic Injection Molding
半岛app体育怎么样好用吗Customers who choose plastic injection molding will find themselves faced with a broad range of terminology that may be unfamiliar.Some standard terms and phrases may include:
- Resin –半岛app体育怎么样好用吗The raw material used in plastic injection molding.
- Colorant –A pelletized or liquid pigment used to produce a specific color in plastic products or parts.
- Mold– A hollow stainless-steel tool that holds molten plastic in a specific form until it dries into a usable part or product.
- Mold cavity –One or more hollow areas within the mold where plastic resin is injected and shaped into the final part.
- Flash and burrs –Protrusions along the parting line or ejector pin, usually caused by excessive pressure or speed.Typically, this is a sign that mold is wearing out or needs to be retooled.
- Runner system –The channels that guide the flow of melted material into the cavities of the part.
- Hydraulic process –半岛app体育怎么样好用吗Most plastic injection molding machines use hydraulic cylinders to press two halves of the mold together at high pressure so the molten plastic can be injected.
- Electric process –半岛app体育怎么样好用吗Electric plastic injection molding equipment uses high-speed servo motors in place of hydraulics, offering improved speed, precision, and energy efficiency.These machines operate more quietly than hydraulic equipment.
- Hybrid process –Hybrid injection molding machines combine the precision, reduced noise, and energy savings of electric machines with the superior mechanical power of hydraulic machines, ultimately providing better performance.
- End-of-Arm Tooling –半岛app体育怎么样好用吗End-of-Arm Tooling (EOAT) refers to robotic arms used in plastic injection molding for a variety of tasks that drastically improve the speed of production and packing.
- Tonnage –Machine presses are rated based on tonnage, or the amount of clamping pressure they can achieve.Press tonnage ranges widely from 5–4,000 tons.
- Hopper and barrel –Hoppers store the plastic pellets used in injection molding processes.The material is fed from the hopper into the barrel, where it is melted prior to injection.
半岛app体育怎么样好用吗Custom Plastic Injection Molding from The Rodon Group
半岛app体育怎么样好用吗With 125 presses at our disposal and a 99.8% satisfaction rating, our manufacturing team can handle high volume custom plastic injection molding projects of any type.We provide the highest quality products and services from our environmentally responsible facility in Pennsylvania.All of our custom plastic injection molded products are proudly Made in America.
半岛app体育怎么样好用吗For more information about The Rodon Group and how we can support your plastic injection molding needs, pleasecontact usorrequest a quote.
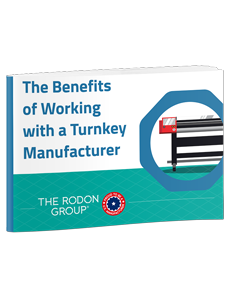
The Benefits of Working with a Turnkey Manufacturer
How to Streamline Your Next Project
In our guide, we explore how a single, experienced team of experts can streamline all aspect of a project's production, including:
- Design Services
- Toolmaking
- Manufacturing
- Order Fulfillment & Bulk Packout